Alloy 20 Swing Check Valve Manufacturer In India
Alloy 20 Swing Check Valve Manufacturer In India
Sachiya Steel International Is One Of The Leading Manufacturer And Exporter Of High Quality Alloy 20 swing check valve in India. recommend the use of these valves in flue gas desulfurization, food processing, and certain pharma operations. They can be hot formed or cold worked. Moreover, they are also used in heat exchangers, condensers, pulp and paper industry, power generation, and so on.
Various alloys are used in manufacturing check valves. One such alloy used to manufacture such valves is the Alloy 20 Check Valve. They contain nickel chromium and molybdenum and are specifically designed to be used in applications that contain sulfuric acid. Moreover, they are also said to resist chloride corrosion cracking and pitting.
UNS N08020 Spring Check Valve is also used in off-shore drilling companies, petrochemical processing, pharmaceutical, seawater, and chemical equipment. These valves can resist acid strikes namely sulfuric acid. Moreover, a minute quantity of niobium can be added to the alloy this enhances the resistance of the alloy to sensitization.
Moreover, the addition of niobium to WERKSTOFF NR. 2.4660 Hydraulic Check Valve also makes it resistant to intergranular corrosion. The alloy used in the production of these valves is said to possess good fabricability. The size of these valves ranges from ½ inch to 48 inches.
Carpenter 20 inline Check Valve is widely used in pickling racks, tanks, food and dying industries, and other environments. These valves have a working temperature ranging from -29 degrees C to +180 degrees C and a size range of ½ inch to 4 inches. The melting point of carpenter 20 valves goes up to 1443 degrees C with a density of 8.1 g/cm3.
Specification Of Alloy 20 Check Valve
BRAND NAME | SACHIYA STEEL INTERNATIONAL |
MANUFACTURER OF ALLOY 20 VALVE SIZE | 1/8″ TO 2″ / 6 MM TO 50 MM |
CONNECTION | THREADED, TUBE END, SOCKET WELD END, FLANGE END |
THREADS | NPT, BSPP, BSPT, METRIC, JIC, UNF |
ALLOY 20 VALVES FLOW PATTERN | STRAIGHT |
BODY SHAPE | HEXAGON |
ALLOY 20 VALVES PRESSURE RATING | 1500 PSI, 3000 PSI, 6000 PSI, 10000 PSI, 15,000 PSI, 20000 PSI |
CRACKING PRESSURE | 0.5 BAR |
ALLOY 20 VALVES ORIFICE SIZE | 2 MM TO 40 MM |
ALLOY 20 VALVES TYPE MANUFACTURER | POPPET TYPE, SPRING TYPE |
MEDIA | HYDRAULIC OIL, AIR, WATER, GAS, STEAM, HOT WATER , COLD WATER , SEA WATER , CHEMICAL |
MEDIA TEMPERATURE | (-50* C TO 350*C ) RANGE AS PER PRESSURE |
BODY TYPE MANUFACTURER | BAR STOCK, FORGED |
ALLOY 20 VALVES PACKING DETAILS | BOX PACKING, WOODEN PALLET |
EQUIVALENT BRANDS | SWAGELOK, PARKER, STAUFF, DK-LOK, HAMLET, OLIVER VALVES, HOKE |
MATERIAL | ALLOY 20 |
Carpenter 20 Check Valve Price In India
Description
|
Price
|
Alloy 20 Corrosion Resistant Flange G non-return Valves | US $ 90-95 / Set |
no. 20 Alloy No8020 Forged reflux Valves | US $ 901 / Piece |
20# Alloy Rotary retention Valves | US $ 1400-2500 / Piece |
Alloy 20 A494 A743 Cn7m Bolted Cover Flanged Non Return Swing Disc foot Valves | US $ 8.0-9.0 / Set |
Alloy 20 Check Valve Manufacturer In India
![]() HIGH PRESSURE ALLOY 20 CHECK VALVE |
![]() INSTRUMENTATION ALLOY 20 CHECK VALVE |
![]() CARPENTER 20 Poppet check valve |
WERKSTOFF NR. 2.4660 Hydraulic Check Valves Seat Materials Options
- PEEK
- Virgin PTFE
UNS N08020 Spring Check Valve Dimensions
Stainless Steel Valves Size
|
Type
|
Cracking Pressure (psi)
|
Weight (lbs)
|
---|---|---|---|
1/2″ | NPT | 0.25 | 1.0 |
1/2″ | NPT | 5.0 | 1.0 |
1/2″ | Socket Weld | 0.25 | 1.0 |
1/2″ | Socket Weld | 5.0 | 1.0 |
3/4″ | NPT | 0.25 | 1.5 |
3/4″ | NPT | 5.0 | 1.5 |
3/4″ | Socket Weld | 0.25 | 1.5 |
3/4″ | Socket Weld | 5.0 | 1.5 |
1″ | NPT | 0.25 | 2.3 |
1″ | NPT | 5.0 | 2.3 |
1″ | Socket Weld | 0.25 | 2.3 |
1″ | Socket Weld | 5.0 | 2.3 |
1 1/4″ | NPT | 0.25 | 3.5 |
1 1/4″ | NPT | 5.0 | 3.5 |
1 1/4″ | Socket Weld | 0.25 | 3.5 |
1 1/4″ | Socket Weld | 5.0 | 3.5 |
1 1/2″ | NPT | 0.25 | 5.3 |
1 1/2″ | NPT | 5.0 | 5.3 |
1 1/2″ | Socket Weld | 0.25 | 5.3 |
1 1/2″ | Socket Weld | 5.0 | 5.3 |
1 1/2″ | NPT | 0.00 | 5.3 |
2″ | NPT | 0.25 | 8.5 |
2″ | NPT | 5.0 | 8.5 |
2″ | Socket Weld | 0.25 | 8.5 |
2″ | Socket Weld | 5.0 | 8.5 |
3″ | NPT | 0.25 | 21 |
3″ | NPT | 5.0 | 21 |
3″ | Socket Weld | 0.25 | 21 |
3″ | Socket Weld | 5.0 | 21 |
Carpenter 20 Check Valves Inspection Points
- Alloy 20 Valves Overall quality inspection (Includes eddy current (non-destructive) electric testing.)
- Dimension check such as lobing, tolerance, out-of-roundness.
- Alloy 20 Valves Material verification
- Final Mechanical Properties
Buy High-Grade Quality from WERKSTOFF NR. 2.4660 Spring Check Valve Suppliers in Threaded/ Tube/ Socket Weld and Flange End Connection
Technical Dimensions Of Poppet Check Valve
![]() Technical Dimensions Of Poppet Check Valve
|
End Connections | Pressure Rating at 100°F (37°C) psig (bar) |
Series |
Dimensions |
||
Size |
Type |
B |
A |
||
1/8 in .0 |
Fractional tube fitting |
6000 (413) |
CH4 |
11/16 |
2 .027 (57 .07) |
1/4 in .0 |
2 .043 (61 .07) |
||||
3/8 in .0 |
CH8 |
1 |
2 .075 (69 .09) |
||
1/2 in .0 |
2 .096 (75 .02) |
||||
3/4 in .0 |
5000 (344) |
CH16 |
1 5/8 |
3 .052 (89 .04) |
|
1 in .0 |
4700 (323) |
3 .088 (98 .06) |
|||
6 mm |
Metric tube fitting |
6000 (413) |
CH4 |
11/16 |
2 .043 (61 .07) |
8 mm |
CH8 |
1 |
2 .070 (68 .06) |
||
10 mm |
2 .080 (71 .01) |
||||
12 mm |
2 .096 (75 .02) |
||||
22 mm |
4900 (337) |
CH16 |
1 5/8 |
3 .048 (88 .04) |
|
25 mm |
4600 (316) |
3 .088 (98 .06) |
|||
1/4 in .0 |
Female NPT |
6000 (413) |
CH4 |
11/16 |
2 .013 (54 .01) |
3/8 in .0 |
5300 (365) |
CH8 |
1 |
2 .055 (64 .08) |
|
1/2 in .0 |
4900 (337) |
1 1/16 |
3 .003 (77 .00) |
||
3/4 in .0 |
4600 (316) |
CH16 |
1 5/8 |
3 .023 (82 .00) |
|
1 in .0 |
4400 (303) |
3 .083 (97 .03) |
|||
1/8 in .0 |
Male NPT |
6000 (413) |
CH4 |
11/16 |
1 .079 (45 .05) |
1/4 in .0 |
2 .017 (55 .01) |
||||
3/8 in .0 |
CH8 |
1 |
2 .036 (59 .09) |
||
1/2 in .0 |
2 .073 (69 .03) |
||||
3/4 in .0 |
5000 (344) |
CH16 |
1 5/8 |
3 .029 (83 .06) |
|
1 in .0 |
3 .067 (93 .02) |
||||
1/4 in .0 |
Female ISO➀ |
6000 (413) |
CH4 |
11/16 |
2 .028 (57 .09) |
1/2 in .0 |
5100 (351) |
CH8 |
1 1/16 |
3 .029 (83 .06) |
|
3/4 in .0 |
4800 (330) |
CH16 |
1 5/8 |
3 .055 (90 .02) |
|
1 in .0 |
4400 (303) |
3 .083 (97 .03) |
|||
1/4 in .0 |
Male ISO➀ |
6000 (413) |
CH4 |
11/16 |
2 .017 (55 .01) |
1/2 in .0 |
CH8 |
1 |
2 .073 (69 .03) |
||
3/4 in .0 |
5000 (344) |
CH16 |
1 5/8 |
3 .029 (83 .06) |
|
1 in .0 |
3 .067 (93 .02) |
||||
1/2 in .0 |
Female SAE/MS |
4600 (316) |
CH8 |
1 |
2 .074 (69 .06) |
1/2 in .0 |
Male SAE/MS |
4600 (316) |
2 .048 (63 .00) |
||
1/4 in .0 |
Male VCO fitting |
6000 (413) |
CH4 |
11/16 |
1 .098 (50 .03) |
1/2 in .0 |
CH8 |
1 |
2 .035 (59 .07) |
||
3/4 in .0 |
5000 (344) |
CH16 |
1 5/8 |
2 .090 (73 .07) |
|
1 in .0 |
|||||
1/4 in .0 |
Male VCR fitting |
6000 (413) |
CH4 |
11/16 |
2 .028 (57 .09) |
1/2 in .0 |
4300 (296) |
CH8 |
1 |
2 .073 (69 .03) |
|
3/4 in .0 |
3700 (254) |
CH16 |
1 5/8 |
3 .078 (96 .00) |
Material Testing Of DIN 2.4660 Valves
- Mechanical Testing
- Alloy 20 Valves Ultrasonic Test
- PMI Testing
- Alloy 20 Valves Flaring Test
- Spectro Tests for Chemical Analysis of the grade
Nickel Alloy 20 Piston Check Valve Dimensions
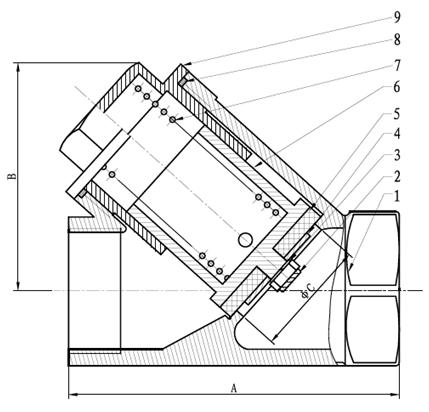
Nickel Alloy 20 Piston Check Valve Dimensions
Valves Size | A | B | C |
---|---|---|---|
½” | 65 | 46 | 19 |
¾” | 80 | 58 | 23 |
1” | 90 | 69 | 27 |
1 ¼” | 105 | 75 | 32 |
1 ½” | 120 | 85 | 41 |
2” | 140 | 98 | 50 |
Applications Of Carpenter 20 Spring Check Valves
- Alloy 20 Valves used in Food and dye
- Pharmaceutical processing
- Alloy 20 Valves used in Chemical and allied industries
- Pickling racks
- Sulfur dioxide (SO2) scrubbers
- Alloy 20 Valves used in Severe environments
- Tanks
CN7M Spring Check Valves Packaging
All wrapped up Alloy 20 valves are pressed to suit the extraordinary conditions for worldwide conveyances and can too customized as per customer’s particular necessities.
Features Of WERKSTOFF NR. 2.4660 Hydraulic Valves
- Ideal fabricability and mechanical characteristics
- Alloy 20 Valves are Sulfuric acid general corrosion resistance
- Welding products minimal carbide precipitation
- Alloy 20 Valves Exceptional stress-corrosion resistance in boiling 20% to 40% sulfuric acid
UNS N08020 Check Valves Dimensions In MM
NPS | Alloy 20 Valves Weight (lb) | G | d | D | C | H | L | f | T | N | M |
---|---|---|---|---|---|---|---|---|---|---|---|
2” | 37.05 | 3.062 | 2 | 5.098 | 4.074 | 5.039 | 8 | 0.006 | 0.063 | 4 | 0.075 |
2-1/2” | 50.07 | 4.013 | 2.05 | 7.001 | 5.049 | 5.087 | 8.05 | 0.006 | 0.071 | 4 | 0.075 |
3” | 63.09 | 5 | 3 | 7.048 | 6 | 6.034 | 9.05 | 0.006 | 0.075 | 4 | 0.075 |
4” | 92.06 | 6.018 | 4 | 9.002 | 7.05 | 9.002 | 11.05 | 0.006 | 0.094 | 8 | 0.075 |
6” | 163.01 | 8.05 | 6 | 10.098 | 9.051 | 10.075 | 14 | 0.006 | 1.002 | 8 | 0.087 |
8” | 238.01 | 10.063 | 8 | 13.05 | 11.075 | 13.043 | 19.05 | 0.006 | 1.014 | 8 | 0.087 |
10” | 390.02 | 12.076 | 10 | 15.098 | 14.025 | 15.087 | 24.05 | 0.006 | 1.022 | 12 | 0.098 |
12” | 621.07 | 15 | 12 | 19.002 | 17.001 | 18.054 | 27.05 | 0.006 | 1.026 | 12 | 0.098 |
DIN 2.4660 Spring Type Check Valves Documentation
- Alloy 20 Valves Destructive Test Report
- Third Party Inspection Reports
- Alloy 20 Valves Non Destructive Test Reports
- EN 10204 3.1
- Chemical Reports
- PMI Test Reports
- Alloy 20 Valves Mechanical Reports
- NABL Approved Lab Reports
- Visual Inspection Reports
- Alloy 20 Valves Mill Test Certificates
Chemical Analysis Of Carpenter 20 Spring Check Valve
Grade | C | Ni | P | Mn | Si | S | Cr | Mo | Nb | Cu |
---|---|---|---|---|---|---|---|---|---|---|
Alloy 20 | 0.02 max | 32 – 38 | 0.02 max | 1 – 2 | 0.7 max | 0.005 max | 19 – 21 | 2 – 3 | 0.1 – 0.3 | 3 – 4 |
UNS N08020 Poppet Check Valve Mechanical Strength
Grade | Melting Point | Density | Yield Strength (0.2%Offset) | Tensile Strength | Elongation |
---|---|---|---|---|---|
Alloy 20 | 1443 °C (2430 °F) | 8.1 g/cm3 | Psi – 35,000, MPa – 241 | Psi -80,000, MPa -551 | 30 % |
Equivalent Material Of UNS N08020 Valve
STANDARD | EN | WERKSTOFF NR. | UNS | AFNOR |
Alloy 20 | NiCr20CuMo | 2.4660 | N08020 | Z2NCUD31-20AZ |
As Manufacturer In India, Don’t Forget To Check Our Material Supplied To Qatar, Malaysia And Other Countries In Europe And America
Philippines, Indonesia, Belgium, Dammam -KSA | Alloy 20 non-return Valves |
Europe, France, Thailand, Qatar | Alloy 20 reflux Valves |
Thailand, Germany, Malaysia, Czechia | Alloy 20 retention Valves |
Bangladesh, USA, Finland, Malaysia | Carpenter 20 foot Valves |
Kuwait, Saudi Arabia (KSA), Brazil, South Africa | UNS N08020 one-way Valves |
Singapore, South Africa, Singapore, Bahrain | WERKSTOFF NR. 2.4660 Hydraulic Valves |
UK, Australia, Nigeria, Philippines | Alloy 20 Instrumentation Valves |
Wafer check valves
Swing check and lift check, whether piston or ball type, tend to require a large amount of body material and can be both bulky, and depending on the body material, expensive. Wafer check valves, however, are slim and can be bolted directly to the receiving flanges through the bore holes on the outer rim of the wafer check valve. This design is lighter, and hence much cheaper when compared to swing and lift-check valves in the same diameter and pressure class.
Ball check valves
A ball-check valve is a check valve in which the ball, sometimes called a lift, can be lifted up off its seat by higher pressure of inlet or upstream fluid to allow flow to the outlet or downstream side. A guide keeps motion of the disc on a vertical line, so the valve can later reseat properly. When the pressure is no longer higher, gravity or higher downstream pressure will cause the ball to lower onto its seat, shutting the valve to stop reverse flow.
Dual plate check valves
Dual plate check valves are designed to overcome the size and pressure drop limitations of the swing and disc type wafer check valves. The flap of the swing check valve is essentially split and hinged down its center, such that the two disc plates will only swing in one direction. The disc plates are held against the seat by a torsion spring mounted on the hinge. In order to hold the hinge in the center of the flow path, externally mounted retainer pins can be used. These retainer pins are a common source of leakage from the valve. An improved design secures the hinge internally, and as the valve mechanism is entirely sealed within the body, leakage to atmosphere is prevented.
The valve is normally closed, as the disc plates are kept shut by the torsion spring. When fluid flows in the forwards direction, the pressure of the fluid causes the disc plates to hinge open, allowing flow. The check valve is closed by the spring as soon as flow ceases, before any reverse flow can occur. The frequent opening and closing of the split disc check valve would soon cause seat damage if the heels of the disc plates were allowed to scuff against the seat during opening. To overcome this, the heel of the disc plates lift during the initial opening of the valve and the plates rotate purely on the hinge as opposed to the seat face.
The split disc type of check valve has several advantages over other types of check valves:
• The split disc design is not limited in size and these valves have been produced in sizes of up to DN5400.
• The pressure drop across the split disc check valve is significantly lower than across other types.
• They are capable of being used with lower opening pressures.
• Split disc check vales can be installed in any position, including vertical pipelines.
Lift check valves
A lift-check valve is a check valve in which the disc, sometimes called a lift, can be lifted up off its seat by higher pressure of inlet or upstream fluid to allow flow to the outlet or downstream side. A guide keeps motion of the disc on a vertical line, so the valve can later reseat properly. When the pressure is no longer higher, gravity or higher downstream pressure will cause the disc to lower onto its seat, shutting the valve to stop reverse flow.
Piston check valves
A piston-check valve is a check valve in which the disc, sometimes called a piston, can be lifted up off its seat by higher pressure of inlet or upstream fluid to allow flow to the outlet or downstream side. A guide keeps motion of the disc on a vertical line, so the valve can later reseat properly. When the pressure is no longer higher, gravity or higher downstream pressure will cause the piston to lower onto its seat, shutting the valve to stop reverse flow.
Pressure seal check valves
Pressure seal construction is adopted for valves for high pressure service, typically in excess of above 170 bar. The unique feature about the pressure seal Bonnet is that the body-Bonnet joints seals improves as the internal pressure in the Valve increases, compared to other constructions where the increase in internal pressure tends to create leaks in the body-bonnet joint.
Relying on fairly simple design principles, pressure seal valves have proven their capability to handle increasingly demanding fossil and combined-cycle steam isolation applications, as designers continue to push boiler, HRSG, and piping system pressure/temperature envelopes. Pressure seal valves are typically available in size ranges from 2 inches to 24 inches and ASME B16.34 pressure classes from #600 to #2500, although some manufacturers can accommodate the need for larger diameters and higher ratings for special applications.
Pressure seal valves are available in alloy grades for over 500 DEG C. The pressure seal design concept can be traced back to the mid-1900s, when, faced with ever increasing pressures and temperatures (primarily in power applications), valve manufacturers began designing alternatives to the traditional bolted-bonnet approach to sealing the body/bonnet joint. Along with providing a higher level of pressure boundary sealing integrity, many of the pressure seal valve designs weighed significantly less than their bolted bonnet valve counterparts.